Electrochemical activation: the first invention
Способ обработки бурового раствора.
Авторское свидетельство СССР № 929682, 1974 г .
Мамаджанов У.Д., Бахир В.М., Шамсутдинова В.Н., Бахир Т.М.
Приоритет этого изобретения по заявке № 2018444 установлен с 22 апреля 1974 года. К этому времени был завершен двухлетний период исследований и промышленных испытаний электрохимических методов и устройств для обработки бурового раствора, которые положили начало технологии электрохимической активации. Эти исследования выполнялись с 1972 года в Среднеазиатском НИИ Природного Газа (СредАзНИИГаз). Буровой раствор - сложная полидисперсная система из частиц глинистых минералов в воде с добавками органических веществ - стабилизаторов, структурообразователей, понизителей вязкости и водоотдачи.
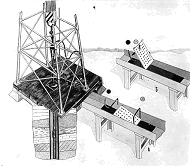
Установка для униполярной катодной электрообработки бурового раствора УОБР (а.с. СССР )
Основной технологической функцией бурового раствора является вынос на поверхность кусочков выбуренной породы с забоя скважины. Глинистые частицы в буровом растворе обычно заряжены электрически отрицательно, при этом плотность заряда зависит от формы поверхности и химического состава кристаллической решетки глинистой частицы, а также от химического состава и концентрации электролитов жидкой фазы бурового раствора. При пропускании тока через буровой раствор на аноде обычно быстро нарастает плотная глинистая корка из наиболее мелкодисперсных и высокозаряженных глинистых частиц. Эта корка препятствует поступлению в буровой раствор продуктов анодных электрохимических реакций, поэтому рН раствора повышается под влиянием катодной, фактически униполярной, электрохимической обработки. Было отмечено, что при одном и том же затрачиваемом удельном количестве электричества, усиление тиксотропных свойств бурового раствора (структурно-механической прочности) при одновременном понижении его динамической вязкости (парадокс) тем больше, чем меньше площадь катода в сравнении с площадью анода. Объяснение этого парадокса заключалось в следующем. Электрические заряды, сосредоточенные на ребрах и заостренных участках крошечных чешуек или иглообразных частиц глинистых минералов, в несколько раз больше, чем заряды на их плоских гранях.

Установки для униполярной катодной обработки бурового раствора УОБР (а.с. СССР № 929682) на буровых месторождений Хаузак, Уртабулак, Зеварды. Узбекистан, 1975.
Под влиянием электрохимической обработки в электрическом поле высокой напряженности у поверхности катода (в области пространственного заряда) возрастала абсолютная величина отрицательного заряда частиц, что приводило к усилению сил отталкивания между ними и, следовательно, к понижению вязкости. Однако, одновременно возрастала также разность потенциалов между ребрами и гранями глинистых частиц, что обусловливало увеличение сил, упорядочивающих структурную организацию взаимодействующих глинистых частиц. Таким образом, структурно-механические свойства бурового раствора усиливались не за счет механического, а за счет электростатического сцепления глинистых частиц. Изучение этого феномена как в лаборатории, так и в условиях реального бурения позволило понять неординарность наблюдаемых процессов, проявляющуюся в неэквивалентности электрохимического и химического методов регулирования и начать попытки практического использования найденного эффекта при бурении нефтяных и газовых скважин.
Наблюдаемый эффект ранее не был известен, поэтому процесс униполярной катодной электрохимической обработки бурового раствора был вначале назван В.М. Бахиром низковольтной поляризацией, а затем, спустя три года - электрохимической активацией. В указанном первом изобретении заявлен способ улучшения параметров бурового раствора без применения химических реагентов путем обработки в технической электрохимической системе, состоящей из источника тока и двух электродов, причем катод имел поверхность меньшую в сравнении с анодом.
Анодом электрохимической системы являлись соприкасающиеся с буровым раствором поверхности циркуляционной системы буровой установки. Практические испытания подтвердили высокую эффективность метода, что выражалось в возможности экономии до 30% химических реагентов, обычно используемых при бурении скважины. Однако выявилось существенное неудобство, связанное с необходимостью периодического удаления глинистой корки с поверхности анода и трудоемкостью этой операции.
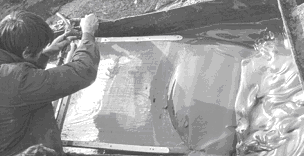
Практическое испытание отрицательного сетчатого электрода для катодной униполярной обработки бурового раствора выявило, что чем больше микрообъемов раствора соприкасается непосредственно с поверхностью электрода, тем сильнее проявляется результат электрохимического воздействия при равных затратах.
Многие последующие изобретения 1974 – 1976 гг были направлены на дальнейшее совершенствование и улучшение найденного метода регулирования параметров бурового раствора и технических систем для его реализации. Устройства, созданные в этот период, имели электрохимические реакторы с плоскими электродами (стальные катоды, магнетитовые или графитовые аноды) со значительной поверхностью единичного электрода (от 0,2 до 0,7 м 2 ), рассчитанные на большие токи (600 - 1500 А) для обработки больших объемов буровых растворов (20 – 90 литров в секунду). В процессе наблюдения за работой опытных образцов установок в условиях бурения глубоких нефтяных и газовых скважин было установлено, что степень изменений в буровом растворе после электрохимической обработки тем выше, чем больший объем раствора непосредственно соприкасается с поверхностью рабочего (отрицательного) электрода. Межэлектродное пространство установок для униполярной (катодной) электрохимической обработки не было разделено диафрагмой. Во всех вариантах устройств, созданных для реализации эффекта униполярного электрохимического воздействия, положительный электрод с образующейся на нем плотной глинистой коркой, был надежно защищен ею от прямого контакта с основным объемом бурового раствора. Продукты анодных электрохимических реакций не поступали в буровой раствор, поскольку накапливались в корке глинистого раствора, толщина которой обычно была в пределах 2 – 3 см .